Technical Blog
The Chemistry of Stainless-Steel Tubing
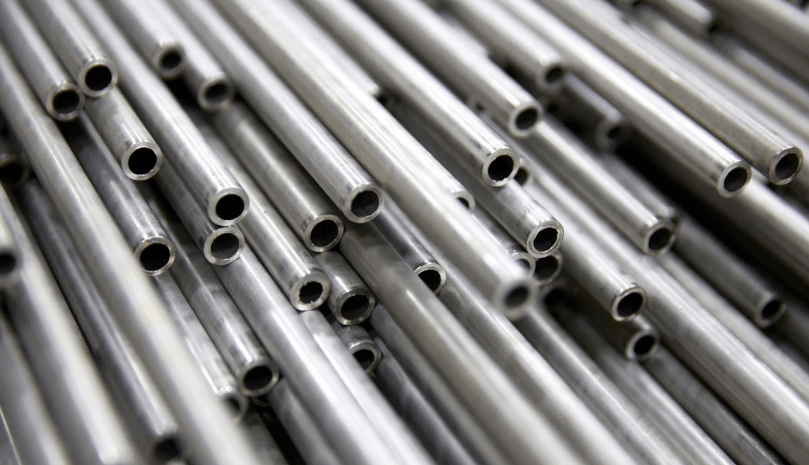
The applications of seamless stainless-steel tubing can include anything from medical equipment to offshore drilling rigs. Selecting the right alloy is one of the ways you can meet your application’s specific requirements and also ensure success on the job. Depending on the alloying elements, you can enhance the properties of your tube—from improving its ductility, to boosting its corrosion resistance. Here’s a rundown of some common alloying elements, including the ways their chemistries affect a tube’s properties:
Nickel Enhances Alloy Ductility
Nickel is the backbone of the Incoloy, Inconel and Monel alloy families and is an additive in austenitic stainless steels. By creating a Face Centered Cubic (FCC) crystal structure, nickel increases the ductility of alloys and is an important component in metals that undergo plastic deformation. Generally, austenitic steels will exhibit impressive ductile properties with only 8% nickel. High-nickel alloys, such as N200 and 52Ni, yield some of the most ductile tubes available.
Chromium And Molybdenum Boost Corrosion Resistance
Known for its corrosion resistance, chromium forms a thin oxide layer on the surface of steel that acts as an outer shell, protecting the metal inside. Most austenitic stainless steels require around 18% chromium to ensure a baseline level of resistance, but some alloys have more.
Molybdenum is especially resistant to chloride attacks and is effective at preventing pitting corrosion in marine applications. You can add molybdenum to nickel alloys to boost their strength and creep resistance at elevated temperatures. Stainless steels, including 316, 317 and 904L, as well as Inconel 825 and 6Mo alloys, are well known for including molybdenum to increase their corrosion resistance.
Carbon Adds Strength
When added to an alloy, carbon atoms settle into the interstitial sites of crystal lattices and alter the way the structure deforms under stress. But while adding carbon to alloys generally makes them stronger, they become more brittle as well. Low-carbon alloys are useful in applications where the tubing will operate at elevated temperatures. Austenitic stainless steels generally contain 0.02–0.08% carbon by weight. Steels like 316, 317 and 304 contain low-carbon variants to increase the alloy’s workability and lower susceptibility to corrosion via sensitization.
To learn more about the chemistry of tubing, download our application note.