Technical Blog
Four Things To Know About Seamless Stainless Steel Tubing
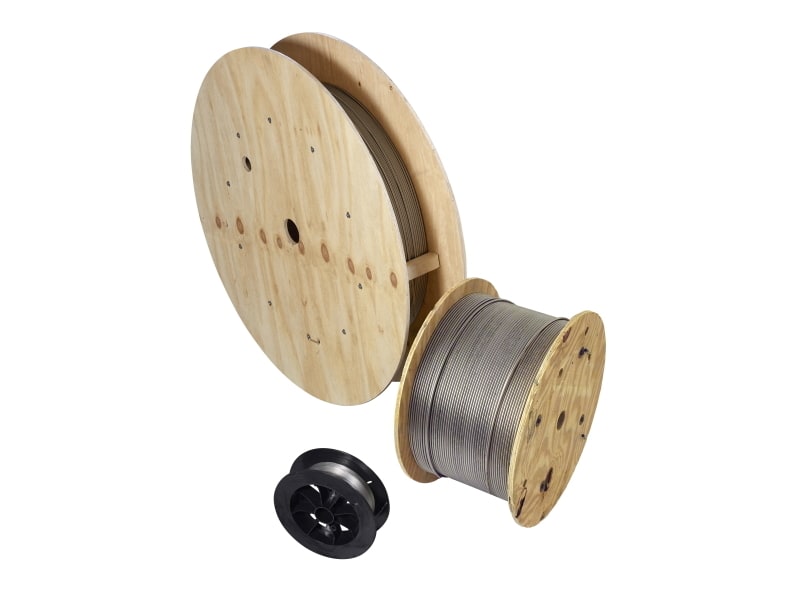
Evaluating various tubing options can be a difficult process. However, the more you consider your options, you’ll find the benefits of seamless tubing hard to beat. For example, this tubing offers exceptional reliability and cost savings for many applications — from solar dishes to hydraulic lines.
Here are four key things you might not know about seamless stainless steel tubing that will help you make the best choice:
1. How Seamless Tubing is Made
Each tube begins as a piece of conditioned steel. Through a process known as extrusion, the steel piece, or billet, is forced through a die to create the desired shape. The steel is heat-treated in a vacuum furnace and worked, cleaned and reworked until it is contracted to an ideal size. Seamless coil tubing can be reduced to the size of a strand of human hair.
2. The Differences Between Welded, Welded-and-Drawn and Seamless Tubing
To produce a welded tube, a flat metal strip is roll-formed and joined with a longitudinal seam. The weld area is often dimensionally inconsistent with the strip, causing areas of stress concentration. These crevices create opportunities for corrosion. Metallurgical contamination during heat treatment can also lead to corrosion due to trapped residue. The result is cracked and ruptured tubing.
Because of the risk of defects due to longitudinal welds, some manufacturers try to minimize the dimensional deviations and re-draw as-welded tubing with various die and plug drawing methods. While these processes — which include welded and drawn, seam-free and seam-integrated — can homogenize the weld when combined with annealing, they need to be repeated several times, adding time and costs to the job.
Seamless tubing, by comparison, is homogeneous throughout the tube cross section and has zero welds, eliminating the potential risks involved with weld seams. Those risks include stress concentrators in high-pressure applications, off-seam welds, weld contamination and corrosion.
3. Popular Applications For Coiled Tubing
Because seamless stainless steel coil tubing offers a low risk of impurities, good corrosion resistance and lower installation costs, it is a preferred choice for many applications, extreme environments and critical industries. For example, it is often used in chemical process and instrumentation applications like steam and heat trace bundles, flow measurement and sensing and fluid and gas transfer. Oil and gas industry uses include control lines, chemical injection and subsea valves. In addition, small-diameter seamless stainless steel tubing can withstand pressures above 30,000 psi for critical applications, making it ideal for gas chromatography (GC) and high-performance liquid chromatography equipment.
Newer applications for seamless coil tubing include compressed natural gas (CNG) transfer for vehicle refueling, hydrogen transfer for material handling applications and firefighter air replenishment systems (FARS). Since seamless tubing doesn’t require multiple fittings, companies can reduce their installation time, labor and costs.
4. Seamless Coil Tubing is Available in Different Forms and Lengths
Did you know that at HandyTube, we can produce seamless coil tubing that can stretch beyond 6,000 feet? That’s more than four times the height of the Empire State Building. In addition, we can provide seamless tubing in many high-performance, corrosion-resistant alloys and sizes in coil or straight form, depending on your needs and application. When the job calls for metal tubing, we can help you select an ideal seamless tube product.
For more information, please contact us.