Technical Blog
Precision Tube ID Surface Condition & Cleanliness: High-Purity Results
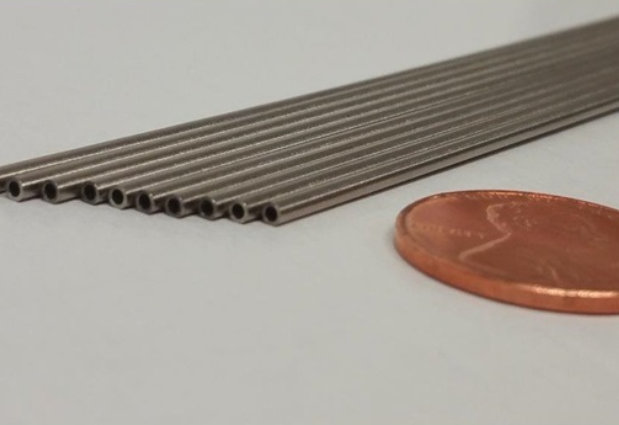
Developers of chromatography, analytical laboratory equipment and medical instrumentation need to ensure they select the correct tubing for their application. The demands of laboratory and production applications require high quality tubing to maintain the critical purity of chemical processes and testing. Tubing that does not meet the stringent specifications of the application typically experience quality problems caused by contaminates. This results in frequent, labor intensive and costly replacement of components because of corrosion of the inside of the stainless steel tubing.
Tubing used in medical and laboratory equipment requires extraordinary cleanliness and surface smoothness of the ID (inside diameter) to ensure high-purity delivery of media (i.e. gases, solvents and chemicals).
Companies in these industries require precision tube that is clean and reliable in the inner diameter. Stainless steel tubing with a clean, burr free and smooth inside diameter can increase cycle time by improving flow rates and eliminating dead zones or volume voids. These problems are not always easily recognizable, but they will show up in the final operating costs and ultimately hurt the bottom line.
Many industries, including manufacturers of processing equipment and medical devices require small diameter, seamless coiled tubing with an outer diameter of < 0.125”. Typically, the OD will range from 0.018” to 0.0625”. However, the purity of medical tubing ID is the important factor of these applications.
The Critical Variable
The surface roughness of the inside diameter is the critical variable. In order to achieve required flow rates and faster sampling cycle times, it is necessary to maintain a controlled, smooth inside diameter surface finish. After many years of extensive R&D, HandyTube has developed processes to support consistently smooth small inside diameters while drawing stainless tubing in coil form. The result is more reliable flow rates and faster sampling cycles with a product that leads the technological evolution of tubular products.
Leading the Technological Evolution
Customers have strict quality control standards that require an in-house ID cleaning process. Typical stainless steel tubing of this type has a rough internal diameter that requires a laborious cleaning process by the OEM/end user.
HandyTube’s proprietary cleaning process, Chroma Clean ID, provides a cleaner inside diameter than other small, critical application seamless tubing. This significantly reduces the amount of in-house cleaning required by OEMs and end users, and provides consistent results every time.
Higher Quality Reduces Labor Costs
The ID cleaning process is more efficient when the tubing has a smoother internal surface that doesn’t harbor voids that hold on to debris and trap contaminants. The internal diameter of this tubing helps increase a facility’s throughput and reduce labor costs in the short and long term.
Tubing suppliers for these critical applications must be ISO 9001:2008 certified and follow other stringent procedures. All manufacturing and quality procedures must be fully documented; including the raw material and the final product, with each order being fully traceable throughout every process. Accompanying specifications, certifications and supporting documents should be kept on file for review by the customer at all times.
Sources: